Buying the latheI picked up an 11" Leblond Rapid Production Lathe at an auction on April 1st, 2005. The auction was really quite a sight, there were tons of older machine tools. Most of them were pretty rusty. There was also a lot of line shafting there. I was there for the entire day on Friday, didn't bid on anything until the later part of the afternoon. Earlier in the day, there were quite a few things that I would have bid on, had I known that I was going to get this lathe. There were two Dumore Versa-mils, nifty lathe attachments that allow you to do milling and grinding on the lathe. I think they both sold for around $75 each. One was somewhat rusty, but the other was in decent shape. There were also some large lathe chucks, toolbits, etc, that I could have picked up cheap. But, at the time those were being auctioned, my only lathe was my 7x12 minilathe, and none of those items could be used on it. Anyway, right before this lathe came up for auction, I won choice on a pallet for $7.50, and picked up a can full of #1 and #2 morse drill collets. I had thought they were regular collets, which would have been nice on my 7x12, but I don't know if I'll ever use these. Might sell them on ebay. So, not too long after those sold, they got around to the LeBlond. They didn't have it out earlier in the day, so not too many people got a close look at it. They pulled it out after some other stuff in the area sold, and the crowd drifted along to what they were selling next. I wasn't particularly interested in that stuff, so I spent some time looking at the lathe. At first, I wasn't interested, because the piece that goes over the top of the rear bearing was missing. However, I looked further, and found that it was in a bucket with some bolts and such. Oh, I should mention that the lathe was taken apart. The carriage and headstock were on the lathe, but the spindle was sitting only halfway into the headstock. The legs were sitting next to it, as was the gear box for the power feed, and a gear box for the motor. So, at first glance it was difficult to tell if everything was there or not. I looked it all over, and found that everything important was there. I bid $50 to start, someone else bid $60, then I bid $70. No more bids, and it was mine. I was excited, but kept doubting as to whether I really got it for $70, or did I miss another number in front of that? Did I somehow end up buying it for $770? After the auction was over (I didn't buy anything else), I went up to pay, and sure enough, it was $70. I was happy to hear that!
Moving the lathe
So, I was now the proud owner of a 1200 lb lathe. How was I going to load it? I had brought along my little
trailer. It's a small trailer, but has been surprisingly useful. And since it is so small I can stand it up on end on the side of the garage, where it takes up little space. Anyway, there was a bobcat with forks available to help load if people needed help, which I thought I'd need to use. However, a kind soul at the auction thought that we could probably slide the bed off the cart it was on (an old railroad baggage cart) right onto my trailer, since they were about the same height. It was heavy, but it worked. With the lathe bed onto the trailer, I wasn't worried about the rest of it. Everything else I coud lift.
My first step to secure the lathe was to screw down some 2x4's that I'd brought along just for that purpose (thanks to my dad who raised me to always plan ahead and be prepared) to the plywood floor of the trailer. These blocks kept the lathe from moving around when accelerating, stopping, and turning. I didn't want the lathe bed sliding into the back of the Forester! Unfortunately, about halfway through screwing the blocks down, my cordless drill died. (At this point I thought it might be handy to convert ad old 12 volt cordless drill that has a dead battery into a corded 12 volt drill that could run off a cigarette lighter socket). I tried using a screwdriver, but there was just no way that I was going to be able to get the rest of the 3" screws in tight enough to hold the lathe in position. I made a few phone calls, and got ahold of my brother-in-law, whom I convinced to bring a cordless drill out to me. He zipped right out there with a friend, and I quickly had the screws in place. After seeing them off, I resumed my loading. With the lathe blocked in place, I started using a few ratchet straps to hold the lathe down. If the blocks could keep it from sliding around, and the straps could keep it from raising up, then it would be solid. A few straps over it, and it seemed to be good. I worked to load the rest of the lathe up onto the trailer. I fit the legs and a motor bracket onto the trailer, and put everything else into the back of the Forester. It was heavily loaded, but I didn't have far to go.
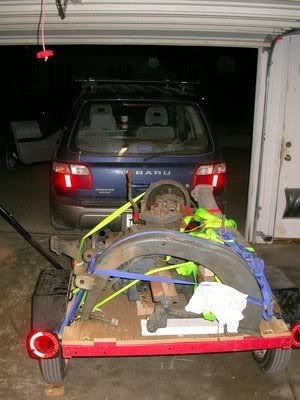
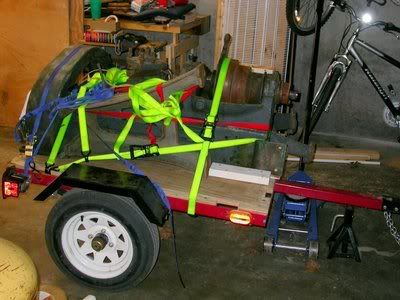
Unloading the latheSo, I had gotten the lathe home, but I now needed someway to unload it. All the pieces, except for the lathe bed, could be lifted off.
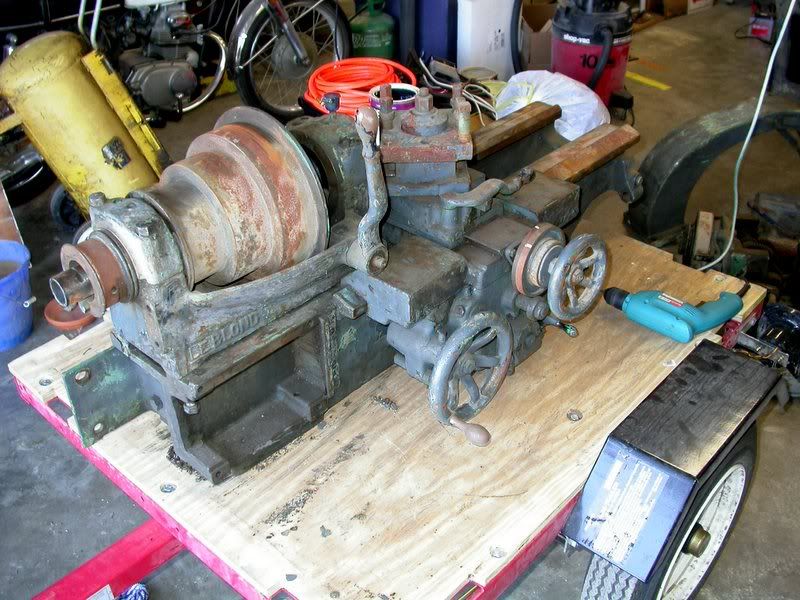
I gave some thought to just borrowing a shop crane from someone, but decided that it was probably best if I purchased one. I figured I'd be using it a lot as I was stripping off paint and getting it set up in my garage. I made a trip up to Harbor Freight to pick up a
folding shop crane. I also purchased a
load leveler while I was there, which was very handy to have. With this, I was able to lift the bed off the trailer.
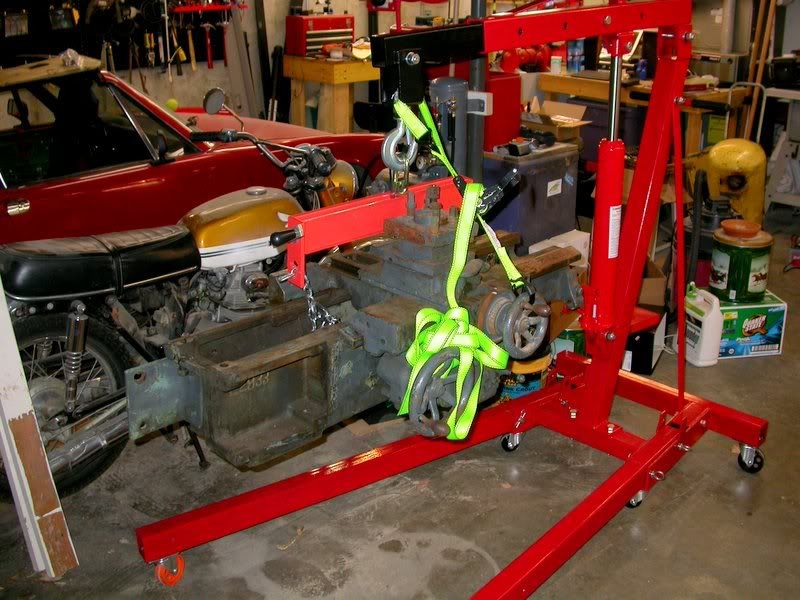
The load leveler and chain lifted most of the weight, but I need the ratchet strap on it to keep it from tipping over. The screw for the crosslide is bent, I think it was bent when I got the lathe, but I'm not sure. I hope I didn't bend it while using it as a lift point. I probably should have figured out a different way to secure it.
Setting up the latheWith the lathe being held by the engine crane, I could attach the legs to the bed. The legs can stand by themselves, so I set one up under the bed, then lowered the bed until it was just above the leg. I bolted the leg to the bed using 3 of the 6 bolts I had gotten with the lathe that appear to be the right ones for this. I then set the other leg under the bed, and did the same. It was soon standing all on its own. I also used the shop crane to put the headstock onto the lathe. That was cool, I felt just like a big crane operator, slowly letting it down, aligning it with the bed.
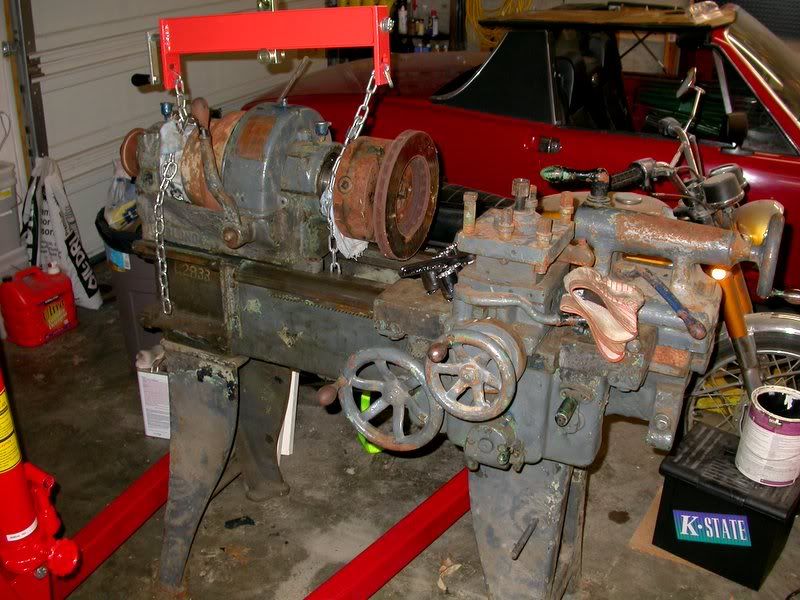
In addition to what was on the lathe, I had quite a few other parts for it:
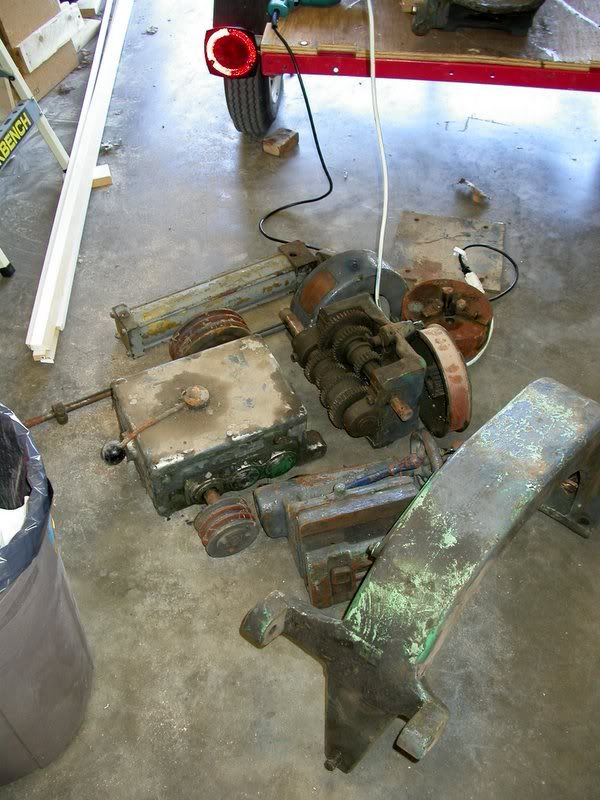
On the top row on the left is a hydraulic cylinder. At some point, the lathe was probably setup with some type of hydraulic automation. I think it bolted to the side of the carriage. May have been used for drilling holes to a set depth. I don't think I'll be putting it back on, I really don't have a use for that function now, and I also don't have all the other parts for that. To the right of the cylinder is a cover that fits on the headstock, and to the right of that is the only chuck I have for it at the moment, a 3-jaw scroll chuck. Right below the chuck is a pulley. The visible part is for a flat belt that connects to the end of the spindle in the headstock. Attached to it (not visible) is a smaller v-belt pulley. Actually, they're both really sheaves, a pulley is a combination of a sheave and a belt. To the left of the sheave is the gearbox that controls the speed of the carriage and crosslide power feeds. This mounts on the front of the lathe bed, under the headstock. The sheave mentioned earlier mounts on the left side of this. Originally, when the lathe was driven from a line shaft, a flat belt would have powered the spindle directly. On the left end of the spindle is a small flat sheave, which is connected via flat belt to the larger sheave shown here. However, when the lathe was converted to use an electric motor, they used the system in reverse. Power is transmitted to the v-belt sheave attached to the flat belt sheave, which then sends power up to the spindle. This is where the gearbox on the far left side of the photo comes in. It was mounted on the support shown in the lower right part of the photo, which mounted on the rear on the left side of the lathe. The motor was connected to the gearbox, which can select among 9 speeds, which is then connected to the v-belt sheave mentioned earlier. Finally, hiding under the gearbox bracket is the tailstock. There is also a chip tray, not shown, that mounts between the bed and the legs. This catches are the metal shavings (swarf), and also catches any coolant, if I'm using it.